Understanding CNC Lathe Machining in Metal Fabrication
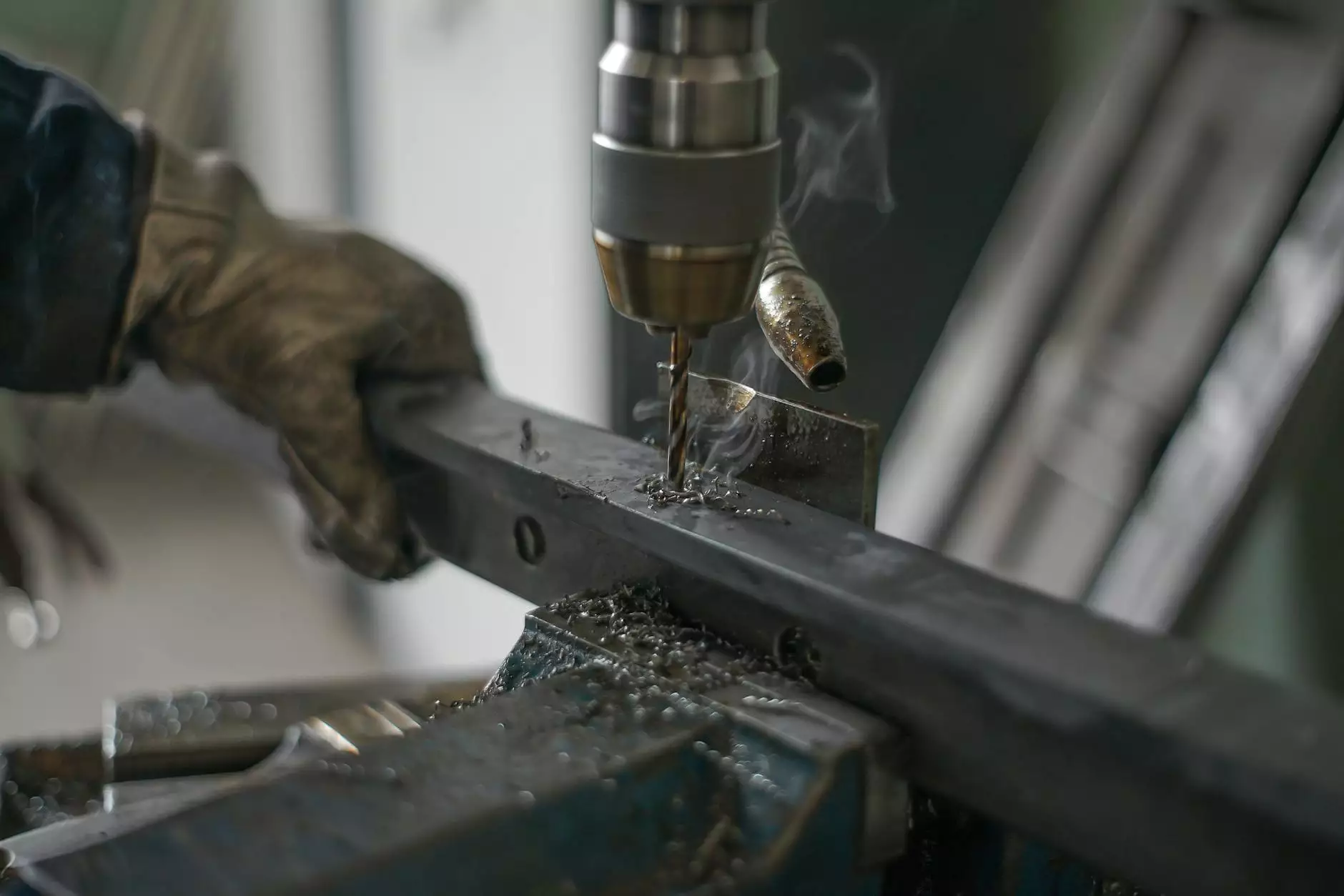
When it comes to metal fabrication, one of the most vital processes employed is CNC lathe machining. In particular, the term "China CNC lathe machining factory" has become synonymous with precision, excellence, and reliability in the manufacturing domain. This article explores the intricacies of CNC lathe machining, its benefits, the technology involved, and the significance of Chinese factories in providing top-notch machining services.
What is CNC Lathe Machining?
CNC lathe machining refers to the process of using computer numerical control (CNC) technology to automate lathe machinery. This method utilizes programmed commands to control the tooling mechanism, resulting in highly accurate and complex designs that can be repeated consistently. Here are the main components:
- CNC Controller: The brain of the operation, interpreting G-code and ensuring precise movements.
- Lathe Machine: The physical machine that performs the cutting and shaping of materials.
- Tooling: Various cutting tools used to shape the material - often tailored to specific operations.
- Material: Typically metals and plastics that are transformed through this process.
The Benefits of CNC Lathe Machining
The advantages of utilizing CNC lathe machining are plenty, particularly when sourced from reputable manufacturing hubs like China:
1. Enhanced Precision and Accuracy
One of the primary benefits is the exceptional precision that CNC technology provides. Since the machinery operates on programmed commands, it minimizes human error and ensures consistent production quality - essential for industries needing tight tolerances.
2. Increased Production Speed
CNC machines can work continuously without fatigue, allowing for faster production times. This increases output and helps manufacturers meet demand effectively.
3. Cost-Effectiveness
By reducing labor costs and minimizing waste through efficient programming, CNC lathe machining helps companies achieve a higher return on their investment.
4. Complex Shape Creation
With CNC lathe machining, manufacturers can create intricate designs and complex shapes that traditional methods cannot achieve, broadening the scope of product development.
The Role of China CNC Lathe Machining Factories
China has firmly established itself as a global leader in manufacturing, particularly in the field of CNC machining. The country's CNC lathe machining factories are recognized for their innovation and ability to cater to large volumes of diverse requirements.
Why Choose China CNC Lathe Machining Factories?
- Quality Standards: Many Chinese factories adhere to international quality standards, ensuring that products meet global specifications.
- Advanced Technology: China is invested in adopting the latest technological advancements in CNC machining, providing cutting-edge manufacturing solutions.
- A Skilled Workforce: With a massive pool of skilled engineers and machinists, Chinese factories offer a high level of expertise.
- Flexibility and Scalability: Many factories can adjust to small or large production runs, allowing for greater flexibility in operations.
Key Technologies in CNC Lathe Machining
Modern CNC lathe machining employs several advanced technologies that enhance efficiency and output. Some of these technologies include:
1. Advanced Materials
Innovation in materials used for machining has led to the development of high-strength alloys and composites, enabling the production of stronger and lighter components.
2. 5-Axis CNC Machining
This state-of-the-art technology allows for more complex machining operations by providing superior maneuverability, offering an edge in highly detailed work.
3. IoT Integration
Internet of Things (IoT) technology is being integrated into CNC machining processes, allowing for real-time monitoring and data analysis, which optimizes performance and minimizes downtime.
The CNC Lathe Machining Process
Understanding the steps involved in the CNC lathe machining process helps in appreciating its efficiency and precision:
Step 1: Design and CAD Modelling
The process begins with designing a component using computer-aided design (CAD) software, which sets the groundwork for the programming stage.
Step 2: Programming
The next step involves converting the CAD model into a G-code, which is a language understood by CNC machines. The G-code directs the machine on how to perform the machining operations.
Step 3: Setup
Before machining begins, operators set up the tool holders, define tooling positions, and ensure the workpiece is securely fastened in place.
Step 4: Machining
Once all setups are complete, the CNC machine begins its operations. The machine executes the programmed commands, shaping the material as specified.
Step 5: Inspection and Quality Control
After machining, inspections are carried out to ensure that the finished product meets the required specifications. Quality control is crucial to maintain standards.
Step 6: Finishing Operations
Depending on the application, finishing operations such as sanding, polishing, or anodizing may occur to enhance the final appearance and properties of the manufactured part.
Applications of CNC Lathe Machining in Various Industries
CNC lathe machining finds applications across multiple sectors, reflecting its versatility:
- Aerospace: Precision machining of components that ensure safety and performance in aircraft and spacecraft.
- Automotive: Manufacturing engine parts, transmissions, and various other critical elements that require precision.
- Medical Devices: Producing high-quality surgical instruments and devices that meet stringent regulatory standards.
- Electronics: Creating components for devices, ensuring tight tolerances that contribute to overall product functionality.
Choosing the Right CNC Lathe Machining Factory
Selecting the appropriate China CNC lathe machining factory can greatly influence your production's success. Consider these factors when making your choice:
1. Experience and Reputation
Research the factory’s history, client testimonials, and case studies to gauge their expertise and reliability in meeting customer needs.
2. Quality Certifications
Ensure the factory holds relevant quality certifications such as ISO 9001, reflecting their commitment to manufacturing excellence.
3. Technology and Equipment
Assess the technology and machinery they employ. A factory with up-to-date equipment is likely to produce higher quality products.
4. Communication and Customer Support
Effective communication is crucial for long-term partnerships. A responsive factory will help address concerns and modifications promptly.
Conclusion: The Future of CNC Lathe Machining
The future of CNC lathe machining, especially from leading China CNC lathe machining factories, is bright. As technology continues to evolve, the industry is bound to witness innovations such as automation, integration of AI, and augmented reality in machining processes. By embracing these advancements, companies can enhance productivity, improve precision, and ultimately provide better products to their customers. For businesses looking to tap into reliable, high-quality manufacturing solutions, collaborating with a skilled metal fabricator like deepmould.net will undoubtedly propel growth and success in today's competitive market.